Customer experiences -NETsystems uses Working Model to explore a complex floating system -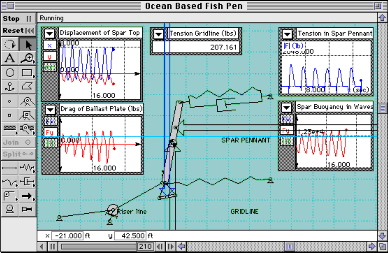
Net Systems of Bainbridge, WA, used Working Model to analyze what effects
ocean currents would have on a spar holding a corner of its sea farming pen in
place. Custom equations apply forces to model the ocean current, spar buoyancy,
and the water's drag on the lower stabilizer disk. A spring/damper is switched
on and off to model the drag the net places on the spar.
Aquaculture -- commercial fish farming
in pen enclosures -- is becoming more prevalent around the world as an important
source of food. The United Nations Food and Agriculture Organization estimates
that by the year 2000 some 25% of total fish landings will be products of
aquaculture. While fish farms inshore are commonplace, offshore aquaculture was,
until recently, a tricky proposition. Recently, one company, with the help of
computers and the latest in desktop engineering software, began modifying
conventional trawling systems and applying the concept to offshore farming.
NETSystems of Bainbridge Island, Washington, has created an innovative open
ocean pen system for raising fish. NETSystems studied the problem of keeping
aquaculture pens stable in rough, open ocean waters for years before hitting
upon the "ocean spar" concept: vertical steel buoys anchored to the
sea bottom that serve as floating fence posts for nets, keeping them relatively
stable through constantly shifting currents. Greater stability to the net pens
means the fish will be less stressed, and the system itself will last longer.
NETSystems is the principal supplier of commercial deep-sea fishing net
products in the North Pacific, including the Gulf of Alaska and the Bering Sea.
The company has diversified to reflect a greater market demand for ocean
farming, forming another company called Ocean Spar Technologies (OST).
Not Just for the Land-locked.
Gary Loverich, chief engineer and part owner of OST, needed a method to test
the stability of his net pen system before deploying an expensive, large-scale
prototype in the deep sea. He saw ads for Working Model, the motion simulation
software from MSC.Software, but assumed that it was only suitable for landlocked
mechanical engineers, not for modeling floating objects at sea. A colleague
convinced him to order the demonstration disk anyway, and Loverich discovered he
could model one of his net pen systems with just the demo copy. His reaction:
"Holy cow." In no time, he purchased his own copy of Working Model for
his Pentium 90 PC.
Whether they are designed by the user in a separate CAD software or within
Working Model's own drafting environment, Working Model applies the laws of
physics to these models depicting the results of its motion analysis with
simulations and graphic data readouts. This kinematics/dynamics analysis
software will reveal whether a design can behave as expected under certain
conditions. Properties such as mass, force, gravity and torque are applied to
any model and then simulations are run to analyze the performance of both
components and entire systems.
Recently, a 1:9 model of the net pen system was jointly tested by Ocean Spar
Technologies and the MIT Sea Grant. The model was instrumented so that Loverich
could gather hydrodynamic information on the system. He incorporated some of
this test data into his Working Model simulations to optimize his sea farming
system.
"There are different characteristics you may enter in a Working Model
simulation; for example, you can enter load as a force or as a drag coefficient
acting on a certain area of the design. So far, I feel most comfortable entering
data as a force that I know is acting on a certain center of effort within the
model." Loverich makes the distinction in the simulation between the center
of effort (where all the force is concentrated) and the center of gravity
because as a wave passes around one spar support of his net system, the velocity
of the water in the wave is maximum at the surface, and decreases farther under
the water, so the majority of the force or center of effort is not at the
mid-point of the spar but toward the surface. Without this data, Loverich cannot
make the best design decisions that will help maintain the shape of these net
pens, especially under very strong currents (e.g., 2.5 knots).
Evaluating Fatigue.
Heavy currents and waves put a lot of fatigue on the net farming system. The
most critical points are the loads on the synthetic mooring lines that retain
the nets' shape while securing them to the spars. "The lines are constantly
fatigued, from zero stress to maximum stress, back and forth," said
Loverich, "and if you bend any wire enough times, it'll break." The
ocean makes this effect even stronger. "Fatigue can happen at much lower
loads than the breaking strength of the material, because the stress load cycles
from zero to maximum so many times when it's in the water." These loads
were measured by Loverich using Working Model.
"What I wanted to find out with these simulations is the orders of
magnitude. Are the waves causing a 10,000-pound load on these ropes, or a
2,000-pound load? I don't need a precise answer, but I need to know if it's plus
or minus 500 pounds. That's as close as I want to get, because I'm going to
overdesign my system anyway for the forces I can't foresee, such as a boat
impact. Working Model can show me which wave frequencies are going to be the
most critical. It's not necessarily the biggest waves -- it might be the
medium-sized waves out of phase that might put on the biggest load."
Once he finds the proper load on the mooring lines, and the acceleration of
the spar, then Loverich exports that Working Model data to his FEA program and
tests the system to make sure the hardware connecting the two components is
strong enough. Loverich uses COSMOS/M to analyze this aspect of his system.
The clarity of its graphical user interface, documentation, and Windows-based
environment made Working Model easy to get acquainted with, and he began to use
it immediately as part of his overall prototype analysis work. "We've
modeled and analyzed our system every way we can, using long-hand static
equations, the ninth-scale model, our FEA package, and now with Working Model.
All of these methods have yielded complementary results, so we feel pretty
confident that we understand the load environment we're dealing with," said
Loverich. Simulating Wave Force. One doesn't actually see waves of water moving
across the computer screen when Loverich runs a Working Model motion simulation.
Instead, a vertical spar or spars float in a coordinate axis system. The wave
force is depicted by an arrow, which increases or decreases as the wave passes.
He measures the tension on the anchor lines, and the velocity of the spar buoys.
"In Working Model I am able to move the connections on the spar buoy to
different locations to enhance the stability of the system. I can move a ballast
weight, the attachment points, anchor lines, and the net, because there are
plenty of attachment points to the buoys." While conducting his wave
frequency simulation, Loverich subjected two linked spars to phased wave loading
(i.e., where the load isn't hitting the spars at the same time).
The waves forced the spars into certain periodic motions, and once that
motion became stabilized, Loverich would end the Working Model simulation.
Depending upon the simulation, that might take just two or three wave crests, or
as high as 20 or 30 wave crests. "I extend the time until I see some
stability," he said. Loverich then analyzed the phasing of the waves and
how it affected the tension values on each mooring line and attachment.
Loverich has also simulated the release of a single spar into the ocean using
Working Model, waiting for it to oscillate to equilibrium where it will sway
equally around its center of gravity. "Waves will cause this type of forced
motion so that it's repeated as long as the wave operates." But Loverich is
also interested in a static simulation of a single spar floating in still
waters. "I have to know how it is going to float in still water, because
that will influence how it acts when waves come by. I used Working Model to
measure the static forces on all the anchor lines. It's a way to calculate the
median load."
Deploying Net Pen System Safely.
The single spar Working Model simulation helped Loverich determine the safest
way to lower the spars into the water, and even answered his questions about how
many workers he can safely afford to fit atop a platform that forms the top of
each spar. He adjusts the ballast weight to make the spar sink to the desired
depth, what is called "freeboard" (the amount of spar above the water
line) and "draft" (amount of the spar below the water line) is at an
optimum ratio. Adding weight to the crow's nest working platform will lessen the
freeboard. Modeling this situation with Working Model is important because
deploying the net pen system safely is half the battle in ocean aquaculture. The
nets, spars, and crane equipment are heavy, so safety is a concern. And Loverich
wants the freeboard to be as minimal as possible in some applications, without
ruining the net pen stability, so that lifting other portions of the net pen
apparatus is not too difficult.
All of these Working Model simulations are critical from a financial
perspective. Deploying such a complex system of spars and nets is difficult at
best in open seas, and the environment plays an important factor in the
execution. If equipment hasn't been tested properly, it can break unexpectedly,
and at inconvenient times. Bad weather can also prevent repairs for days or
weeks, time that is money to any fishing operation. Loverich estimates that it
costs 40 times as much to repair something at sea than in the shop. By using
motion analysis, he is decreasing his risk and increasing the dependability of
his product.
Ocean Spar Technologies will use Working Model not just to perfect the net
pen system but to continually customize it for different fisheries around the
globe. Ocean Spar will keep various net pen models in the simulation files, and
when a customer supplies local tidal and current information, or requests a
different net pen configuration, Ocean Spar will be able to input the variable
data and learn what adjustments will have to be made to customize the product
accordingly. "Our engineers will call up Working Model and put in the local
parameters and then we'll simulate the motions and forces that might impact our
system."
Kinematics/dynamics simulation is saving Ocean Spar Technologies money as
well as time. The time to market this complex and vital product has been slashed
because of the help Working Model has provided in simulating the motions and
forces that will affect this innovative product. And Working Model helped
explore a complex floating system, not just single land-based masses -- a
flexibility that was employed to great advantage by this company. By continuing
to employ Working Model simulations, Ocean Spar will retain its competitive edge
in the ocean aquaculture market while improving the ability of people worldwide
to sustain their own fish farming industries. |